Institute of Metallic Biomaterials
Human life expectancy is increasing, and more and more people go in for high-risk sports. Against this background, the Institute of Metallic Biomaterials develops novel materials for medical implants based on titanium and magnesium. One target is to improve biocompatibility of permanent titanium implants by developing non-toxic alloys and adapting the materials to the mechanical properties of the bone. Another focus is laid on magnesium alloys that degrade over time in the body. By adding pharmaceutically active elements, such as antimicrobial silver, to the alloys novel regenerative or therapeutic effects are intended to become effective during magnesium degradation. Our work covers the entire process chain, including studies in animal models as well as the intensive utilization of in situ methods.
CAU, Hereon and UKSH agree on cooperation for digital implant research
Kiel University (CAU), the Helmholtz Centre Hereon and the University Medical Centre Schleswig-Holstein (UKSH) are joining forces in the field of digital implant research. The aim of this interdisciplinary project is to take implant development to a new level by combining biomaterial research, data science, AI and medical research.

Confident and full of anticipation after the successful founding symposium on 10 June 2024 in Kiel: The members of the founding team (from left to right) Prof. Cyron, Prof. Checa, Prof. Jansen, Prof. Saalfeld, Prof. Deuschl, Prof. Willumeit-Römer and Prof. Quandt. Further founding team members (not pictured): Prof. Tomforde and Prof. Popp.
Prof. Dr. Regine Willumeit-Römer, co-initiator of the collaboration and Director of the Institute for Metallic Biomaterials at Hereon: "The future of implant development lies in the use of computer simulation models and artificial intelligence, which map the complicated development cycle from material to tissue regeneration and ultimately flow into the authorisation process. In this way, existing implants can be improved and further developed into personalised implants based on individual, molecular body characteristics." The research centres on digital twins that depict physiological and material science conditions in computer models.
With the help of these digital twins, new implants are no longer developed at the workbench, but on a high-performance computer and are no longer heuristically acceptable, but comprehensively optimised to meet medical needs.
The contribution of the Institute of Metallic Biomaterials lies in the provision of data on Mg-based and thus degradable implants in a biological environment, the realisation of corresponding experiments and simulations. Prof Willumeit-Römer also acts as project coordinator.
DAAD Rise scholarship holder Janice Xie at MBB

Janice Xie (Photo: Heike Helmholz)
Janice Xie is a student at Northwestern University in Illinois, USA, studying materials science and engineering with a focus on biomaterials. During her time with us, she researches the foreign body reaction on Mg-Li alloys.
more (Intranet Hereon)
Bridging the gap between in vitro and in vivo degradation rates for Mg-xGd implants

The degradation rate calculated using the surrogate model in comparison to the experimental data. Volume renderings are inserted for samples after 4 and 8 weeks of degradation
Is it possible to predict in vivo degradation of magnesium implants based on their in vitro degradation? In our recent publication “Utilizing Computational Modelling to Bridge the Gap between In Vitro and In Vivo Degradation Rates for Mg-xGd Implants”, we built a surrogate model that is trained on a more computationally expensive computer model. By calibrating the surrogate model to datasets from in vitro and in vivo degradation of magnesium-based screws, we have been able to find a parameter with which we can map one to the other. In this case, we can link the diffusion rates of Mg2+ ions in the different systems. In the future, it may become possible to estimate degradation rates in vivo by leveraging such links between diffusion rates derived from in vitro and in vivo experiments through surrogate models. This enables to draw conclusions about in vivo degradation rates solely from in vitro experiments.
Al Baraghtheh et al., Corros. Mater. Degrad. 2023 4(2):274-283
Publication selected as Editor’s Choice: In Situ Synchrotron Diffraction Study of Compression of AZ91 Composites Reinforced with Recycled Carbon Fibres

Macroscopic true strain (left), strain on lattice planes (centre), and intensity (right) against true stress for AZ91/C100/5f in as extruded state
Sustainability is an important consideration for manufacturers. One approach to improve on sustainability in the automotive and aerospace industries is to improve fuel efficiency by using lightweight materials. Magnesium is a promising candidate for these applications as it is lightweight, has a high specific strength, good machinability and castability. Alloying additions can further improve these properties as well as improving corrosion resistance and ductility. Metal-matrix composites (MMCs) using an Mg alloy matrix offer improved mechanical properties, whilst retaining Mg alloys’ light mass. Sustainability can also be considered when choosing the reinforcing addition. Recycled carbon fibres (rCFs) recovered from carbon-fibre-reinforced polymers maintain many of the mechanical properties of virgin CFs, but are cheaper and less energy intensive to produce. Finding uses for rCFs will also encourage more commercial recycling of carbon fibre reinforced composite materials. The colleagues of our Institute, with partners from the Institute of Material and Process Design and the University of Cambridge, utilized synchrotron radiation diffraction to understand how the heat treatments and CF reinforcement affect the active deformation mechanisms during to develop high-performance, sustainable composite materials. The corresponding publication has been selected as an Editor’s Choice Article in Crystals.
Mance et al., Crystals 2022 12(11):1502
Helmholtz Imaging Best Scientific Image Contest 2023: 1st Place in the category participants choice award

Magnesium Watercolour Whirl by Sarkis Gavras (Hereon)
Sarkis Gavras won the first place of Best Scientific Image Contest 2023 in the category “Participants’ Choice Award” with his image of a Magnesium Watercolour Whirl. This polarized light optical image shows a magnesium alloy with a colorful array of small grains, which have formed along the edge of a swirl shaped pore.
Best Scientific Image 2023
Structure and Mechanics of Bone Depend on Implant Materials
How do we study the behavior of bone implants under load in a realistic environment that responds to the implanted material? In our recent publication “On the material dependency of peri-implant morphology and stability in healing bone” the imaging capabilities of the beamlines operated by Hereon at DESY were combined with a miniaturized loading cell and high-performance digital volume correlation software to answer such questions with 4D imaging.
We were able to visualize the strains in the bone surrounding several screw implants experimentally on the micrometer scale. The study demonstrates that these strains and the morphological parameters that are relevant to the expected implant stability depend on the biomaterial deployed. Thus, we expect that the choice of material for the bone implant of the future will not just be a choice between one or two materials but depend heavily on the shape of the fracture and patient bone health.
Bruns et al., Bioactive Materials 2023 28:155-166
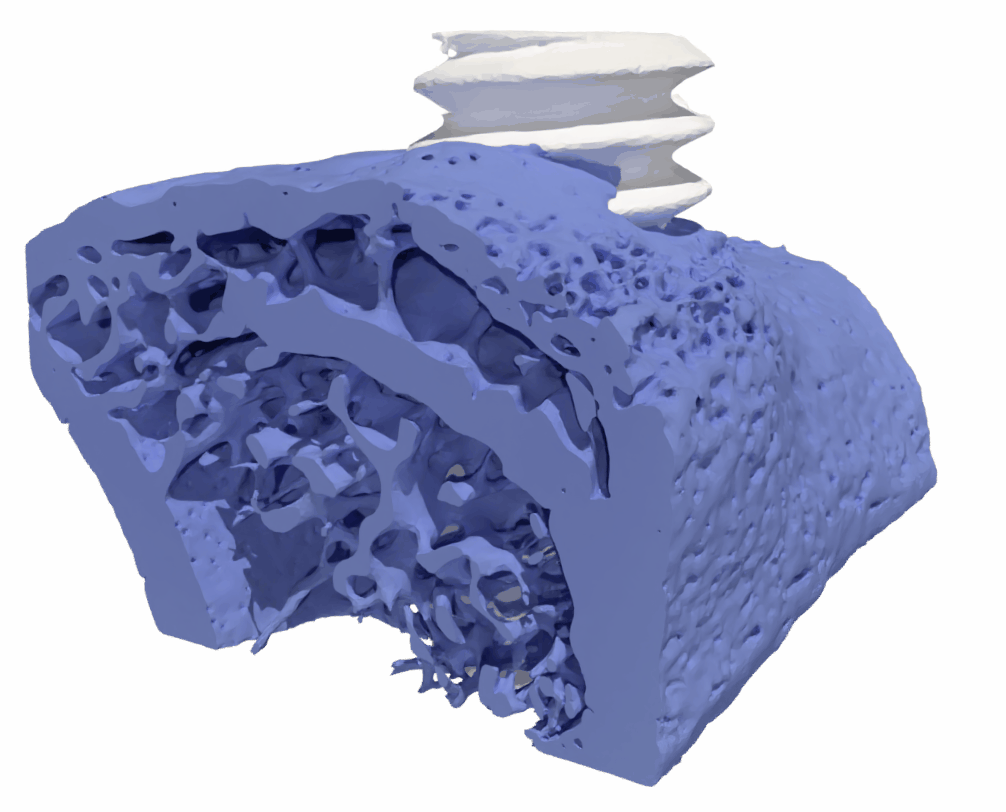
Rendering of bone deformation determined from a push-out sequence. Color indicates the deformation magnitude.
Magnesium: Solutions in Medicine
360°- clip, photo feature, videos (German only) and further information
link