Equipment
The equipment of the department reflects its holistic approach to consider all aspects of the investigated membrane processes.
Medium scale membrane casting facility
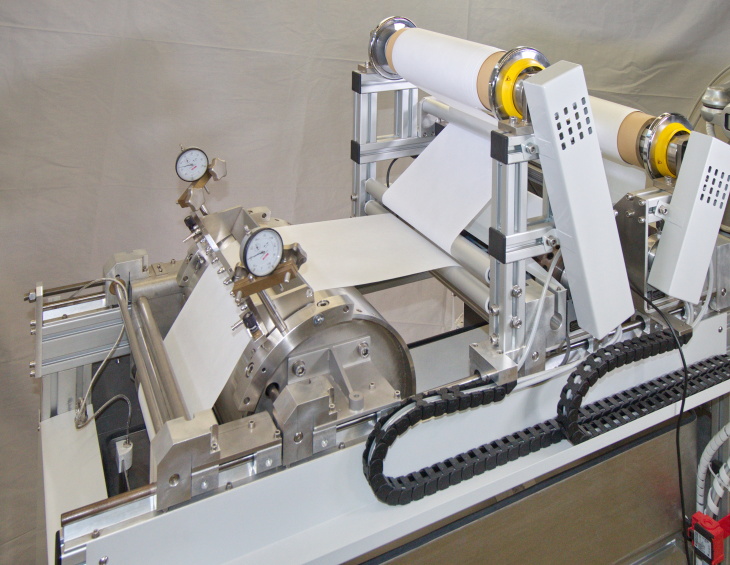
Image: Hereon/ S. Shishatskiy
Purpose:
Formation of test batches of porous or integral asymmetric membranes at close to industrial conditions. On this device a polymer solution is deposited a non-woven support and immersed into a coagulation bath (water or water with ethanol). For example: ultrafiltration membranes made through a combination of self-assembly of amphiphilic block copolymers and the non-solvent induced phase separation process (SNIPS).
Features:
o Batches from 20 cm long, 10 cm wide and up to 200 m in length and 28 cm in breadth are possible
o Casting speed up to 4.4 m/min
o Pre-set tension up to 50N
o Fume capture in case of volatile solvents
Pilot scale membrane casting facility

Images: Hereon/ S. Shishatskiy
Purpose:
Formation of enlarged batches of membranes by SNIPS leading to porous and gas selective integral asymmetric membranes.
On this device polymer solutions are casted on a non-woven support and immersed in a coagulation bath (typically water) in pilot scale to produce micro or ultra filtration membranes and support membranes for TFCM. It also possible to produce integral asymmetric membranes for gas separation applications.
Features:
o Batches up to 300 m length and 70 cm breadth are possible
o Casting speed 0.1-6 m/min
o Bath temperature range 5-40°C
o Bath volume 4 m3 allows for formation of several membrane rolls per day.
Pilot scale membrane coating facility I for thin film composite membranes (TFCM)
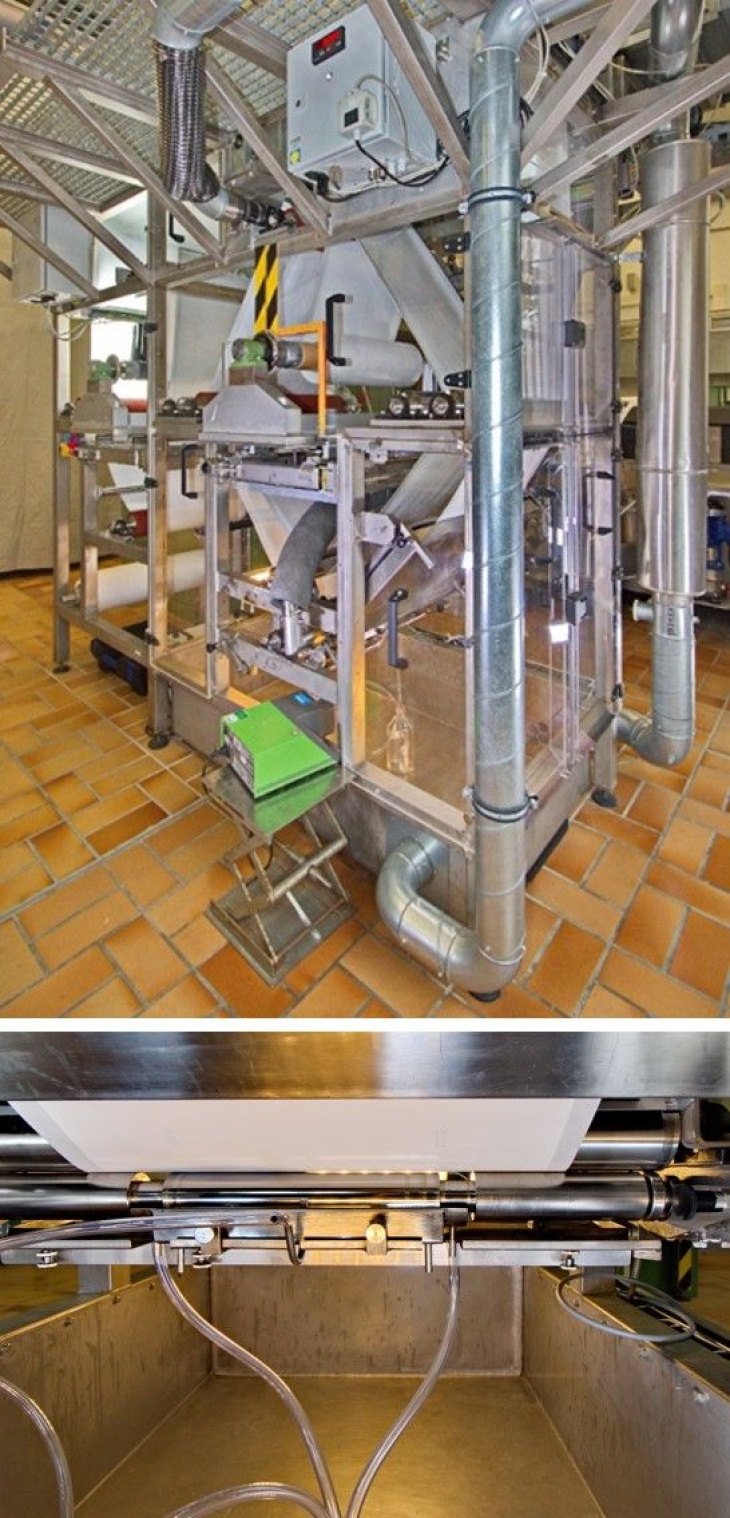
Images: Hereon/ S. Shishatskiy
Purpose:
Formation of single and multilayer TFCMs in experimental and semi-industrial scales.
Support membranes can be coated with diluted polymer solutions to produce TFCM with selective layer as thin as 70 nm
After polymer solution deposition membranes are treated in an oven in order to evaporate solvents and to provide conditions for cross-linking reactions
Features:
o Batches up to 250 m length and 60 cm breadth are possible
o Oven up to 150 °C
o Coating speed 0.1 – 5 m/min
o Reservoir of coating solution can be filled by a peristaltic pump
o Automatic acquisition of process data for monitoring, e.g. mass consumption and coating speed possible
Membrane coating facility II for thin film composite membranes (TFCM)
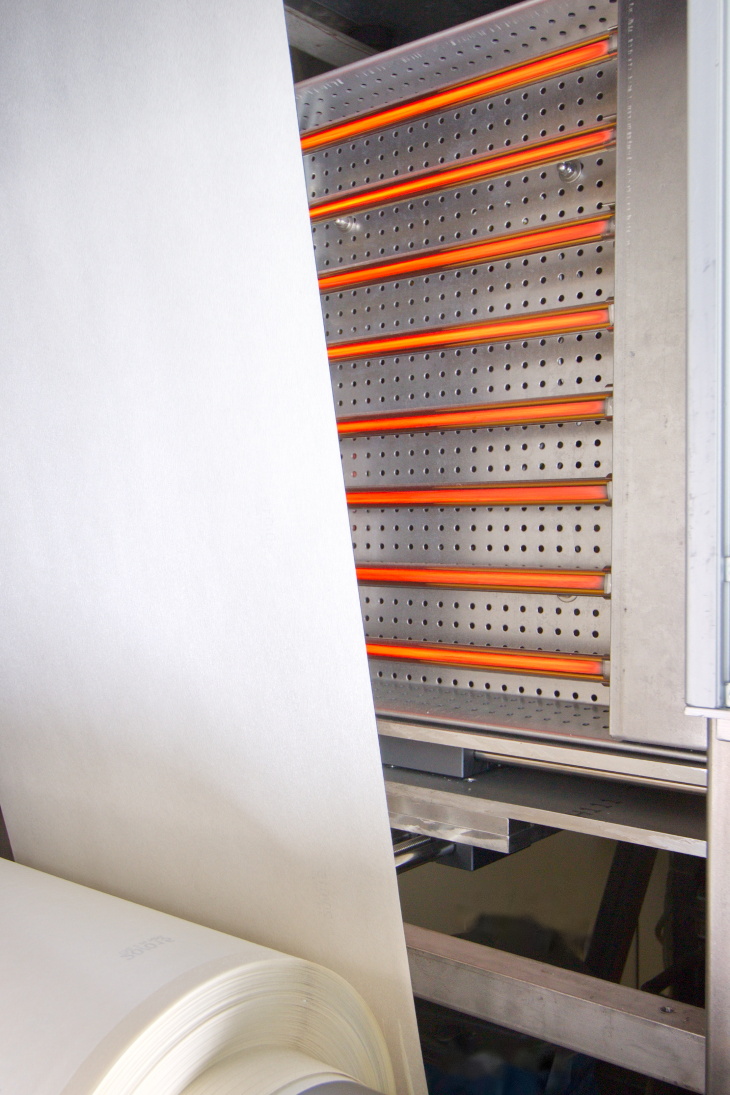
Image: Hereon/ S. Shishatskiy
Purpose:
Formation of TFCMs with special properties
Coating of support membranes with diluted polymer solutions to produce TFCM as thin as 70 nm, solvent evaporation in standard oven and IR irradiation as post-treatment for selective layer cross-linking or thermally induced modification
Features:
o Batches up to 250 m length and 45 cm breadth are possible
o Coating speed 0.1-0.65 m/min
o Reservoir of coating solution can be filled by a peristaltic pump
o Oven up to 210 °C
o IR lamp provides temperature on the selective layer surface above 250°C.
The department of Process Engineering designs and builds membrane modules with new developed membranes for technical applications. This combination of polymer chemistry (developing of selective layer materials) and process engineering (building modules and realizing projects) is the key of success of the Hereon membrane technology. At Hereon modules with membrane areas up to 75 m2 and packing densities of up to 900 m2 membrane area/m3 module volume are examined.
100 mm diameter envelope type module with up 1 m2 membrane area
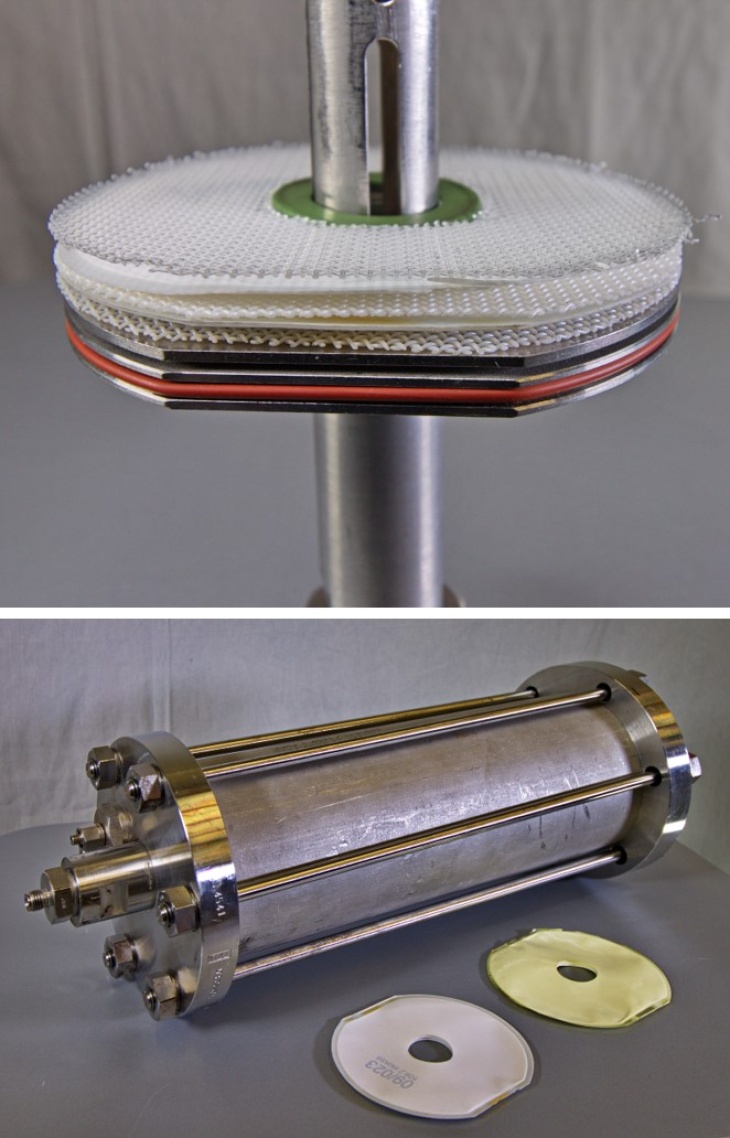
Images: Hereon/ S. Shishatskiy
100 mm diameter envelope type module with up 1 m2 membrane area
Spiral wound element for mini plant applications
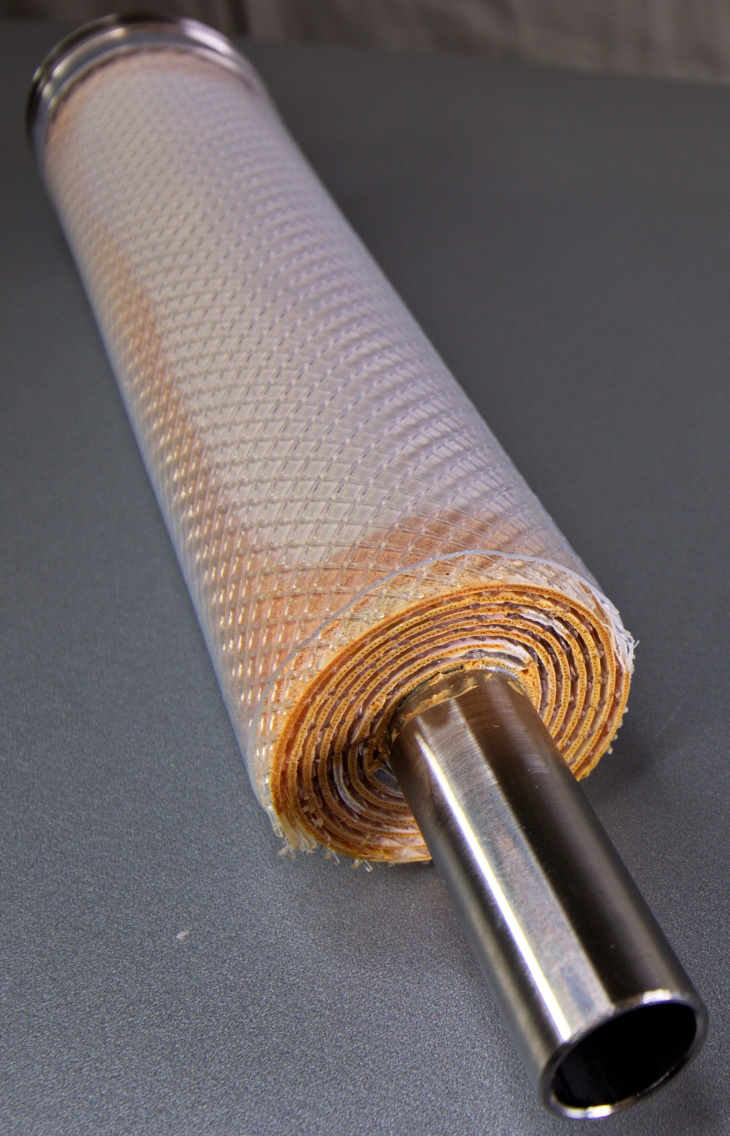
Image: Hereon/ S. Shishatskiy
Spiral wound element for mini plant applications
Envelope type membrane modules for gas separation applications
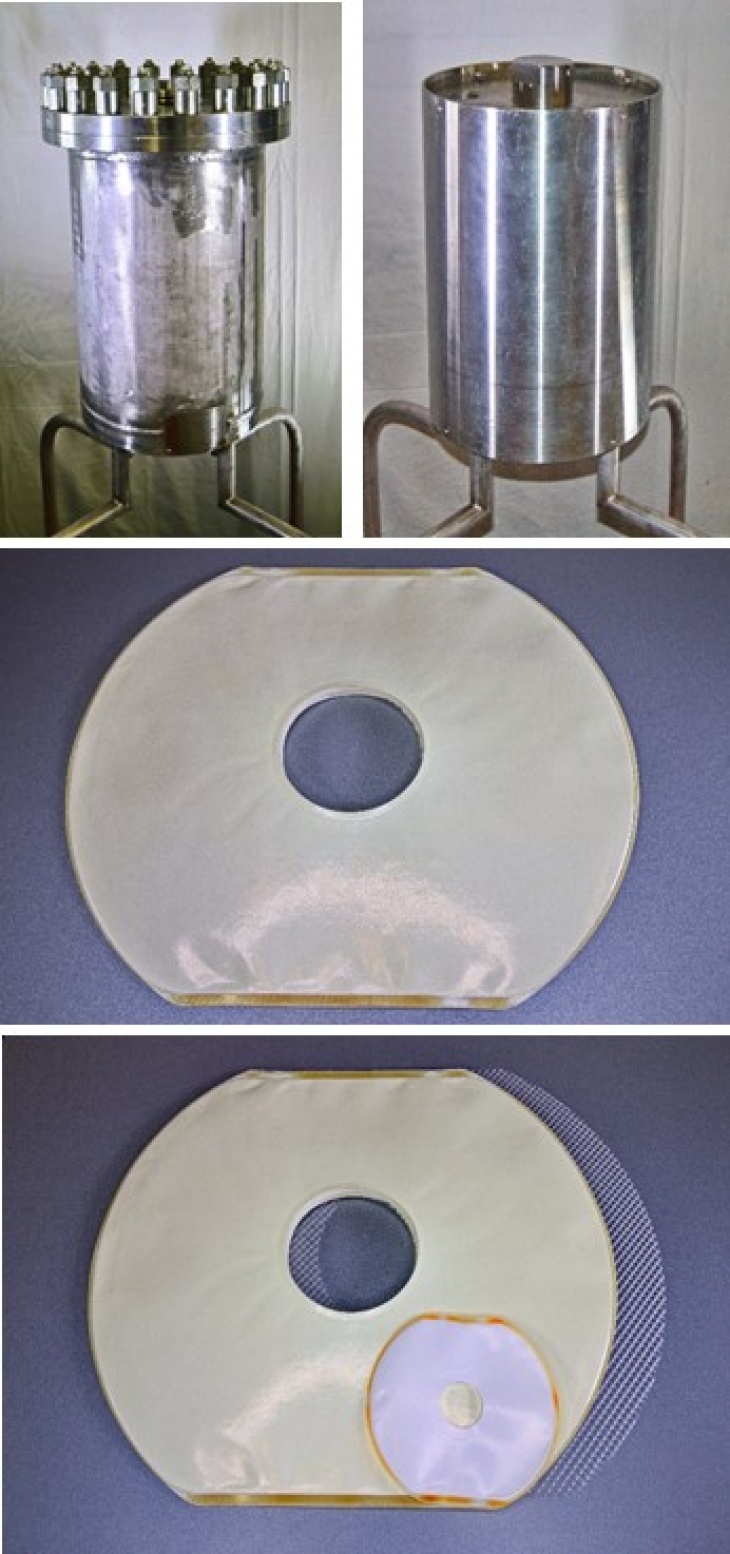
Images: Hereon/ S. Shishatskiy
Envelope type membrane modules for gas separation applications
Counter current experimental membrane module and rectangular membrane envelope
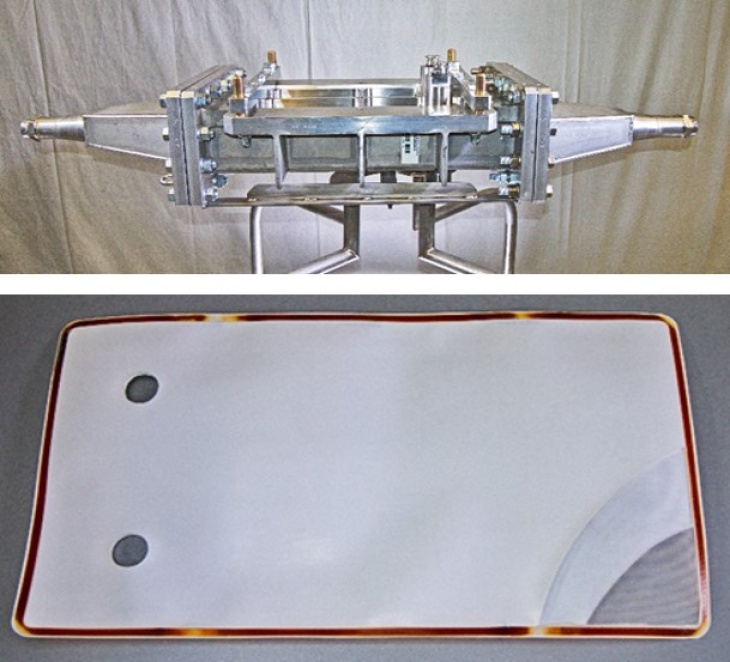
Images: Hereon/ S. Shishatskiy
Counter current experimental membrane module and rectangular membrane envelope
The department of Process Engineering within the Institute of Membrane Research at Helmholtz-Zentrum Hereon has a long experience in the design of membrane modules and plants for membrane based separations.
Time Lag
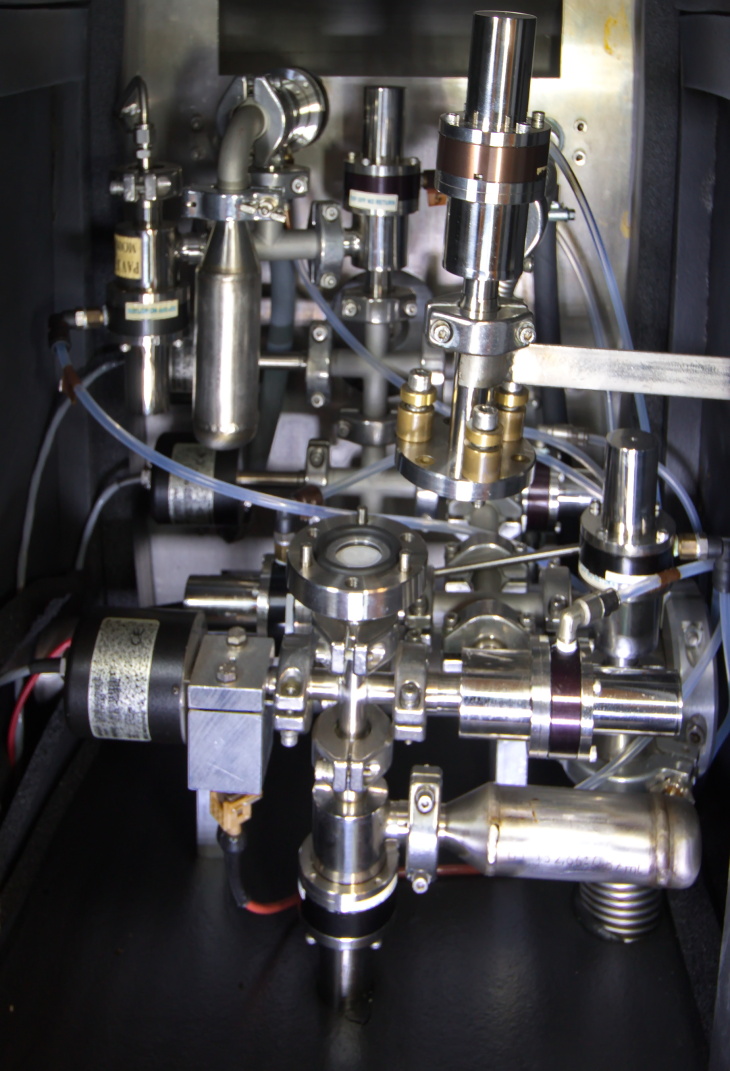
Image: Hereon/ S. Shishatskiy
Purpose:
„Time-lag” facilities based on the “constant volume / variable pressure” principle are designed for investigation of gas and vapour transport properties of polymers or other materials that form dense films. Permeability, diffusion and solubility coefficients can be determined for up to 15 gases or vapours in a wide temperature range. These results are the basis for identification of materials suitable for further conversion into membranes.
Features:
o 15 connections for gases and vapours at room temperature, 1 vapour connection for containers conditioned to the temperature and pressure of the measurement cell
o Membrane area: variable from 0.5 cm2 to 13.4 cm2
o Temperature: from 5 °C to 130 °C
o Feed pressure: from 20 to 1200 mbar abs.
o Permeate pressure: from 0.01 to 10 mbar
o Vacuum: turbomolecular pump, sample evacuation at <0.001mbar
o Software: Hereon developed software for fully automatic control of the time-lag facility.
Pressure Increase
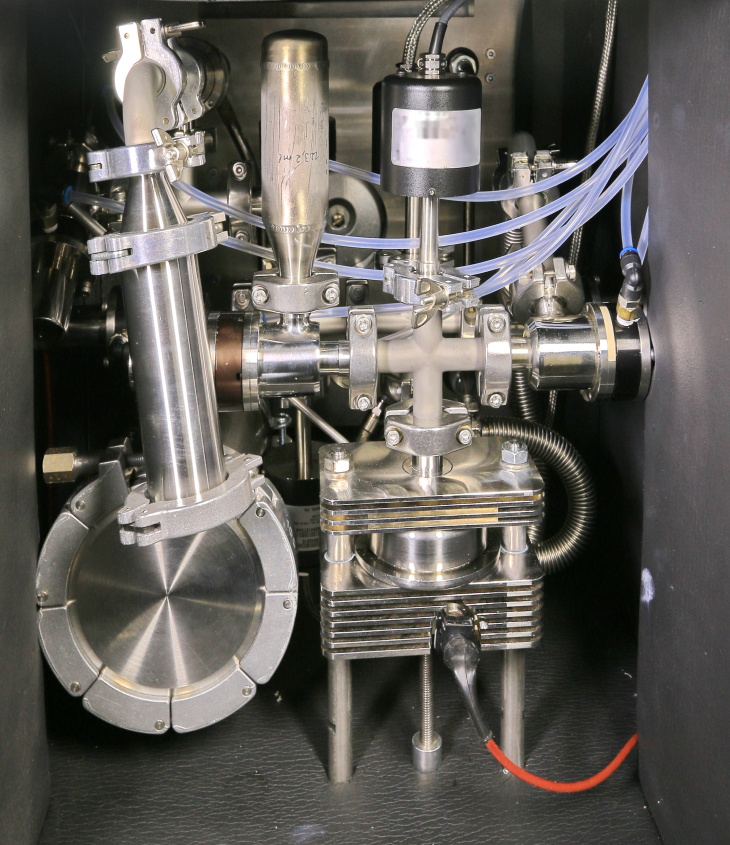
Image: Hereon/ S. Shishatskiy
Purpose:
The facility utilizes the „constant volume / variable pressure“ approach of gas transport properties investigation.
The aim, in contrast to the “Time-lag” facility is to investigate performance of highly efficient membranes for gas separation, and to provide a set of experimental data for membrane separation process modelling.
The properties are investigated in dependence on feed pressure, permeate pressure, temperature and time (aging)
In-house developed facility control software allows for programmed, reproducible sample properties investigation.
Features:
o Feed pressure range 50 to 1200 mbar
o Permeate pressure can be varied in ranges 0-13 mbar and 0-130 mbar depending on pressure sensor
o Temperature range 5 to 130 °C
o Calibrated to <0.5% accuracy for permeate volume ensuring high accuracy of results
o 15 gas and vapour connections at room temperature
o Thermostated feed pressure vessel of 2000 cm3
o 1 thermostated pressure vessel for vapour transport investigation
o For flat membrane with 0.5 to 34 cm2 active area
o For hollow fibers with wide membrane area range 0,1 to 100 cm2
o Measurement cell is designed for fast sample change, especially designed membrane holders allow for multiple test of the same membrane sample to follow membrane changes in time or due to influence of other physical or chemical factors.
Wide pressure and temperature range facility“Arrhenius”
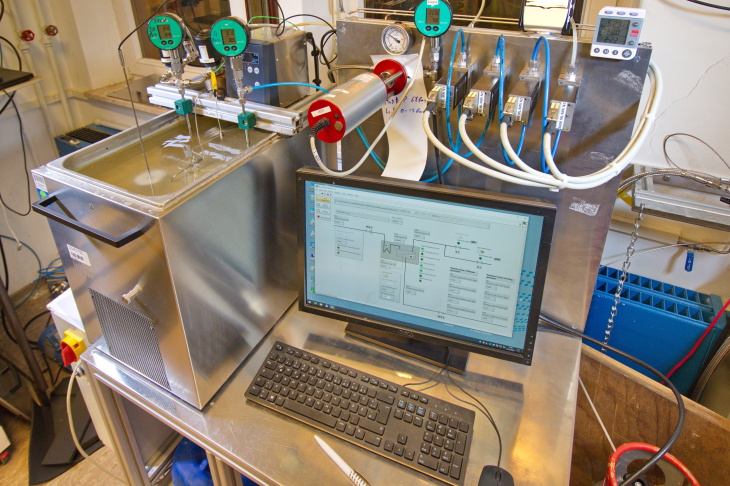
Image: Hereon/ S. Shishatskiy
Purpose:
Investigation of gas and vapour selective membranes over wide temperature ranges under the influence of condensable penetrant activity from 0.1 to 1. Condensation of penetrant on the feed side of the membrane is possible.
Facility utilizes „variable volume / constant pressure“ approach of gas transport properties investigation.
Features:
o Feed pressure range 1 to 63 bar abs.
o Permeate pressure 1 bar abs.
o Temperature range -20 to 110 °C
o Direct connection to gas bottle
o Electromechanical pressure regulator allows for >400 pressure steps
o Permeate pressure can be automatically controlled
o Accurate temperature control
o Permate flow measurement via 4 high precision mass flow sensors
o In-house developed facility control software allows for programmed, reproducible sample properties investigation in dependence of feed pressure and temperature
Membrane envelope quality control facility
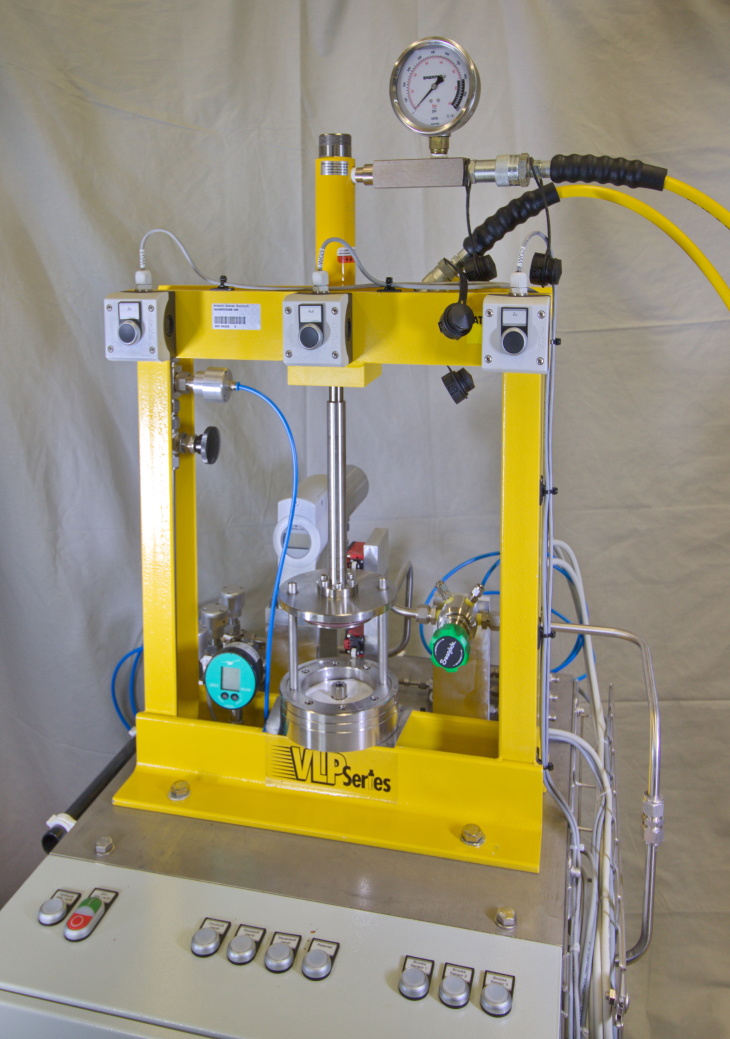
Image: Hereon/ S. Shishatskiy
Purpose:
Quality tests of membrane envelopes for 100 mm and 310 mm diameter membrane modules.
Features:
o Envelopes are easily exchangeable
o Quality control by permeation of pressurized or synthetic air
o Feed pressure and feed-retentate flowrate can be adjusted according to membrane envelope performance
o Permeate flowrates of O2 and N2 are measured by combination of O2 sensor (0-100 mol%) and mass-flow sensor, resulting in accurate permeance and selectivity measurements
Mixed gas facility for membrane investigation
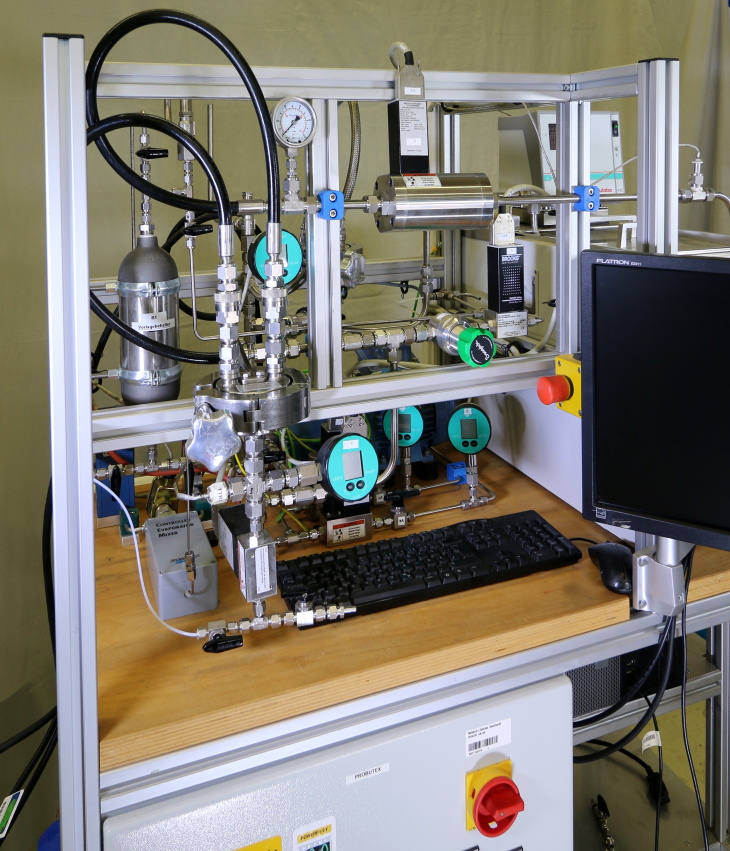
Image: Hereon/ S. Shishatskiy
Purpose:
The facility is designed for long-term investigation of membrane samples at mixed gas separation conditions. It utilizes „variable volume / constant pressure“ approach of gas transport properties investigation. The main feature of the facility is the circulation of the gas mixture in the feed side loop and automatic compensation of feed gas mixture consumption due to permeation through the membrane
Features:
o Membrane area from 1 cm2 to 34 cm2 flat sheet membrane samples.
o Feed gas pressure up to 35 bar abs, pressure provided from the gas bottle.
o Possible use of penetrants being liquid at room temperature
o Operating temperature is room temperature
o Feed side linear velocity of the gas stream can be varied for investigation of concentration polarization effects
o Atmospheric pressure on permeate side
o Feed, retentate, and permeate gas mixture compositions by gas chromatography, infrared sensors or mass spectroscopy
Mixed gas high temperature facility
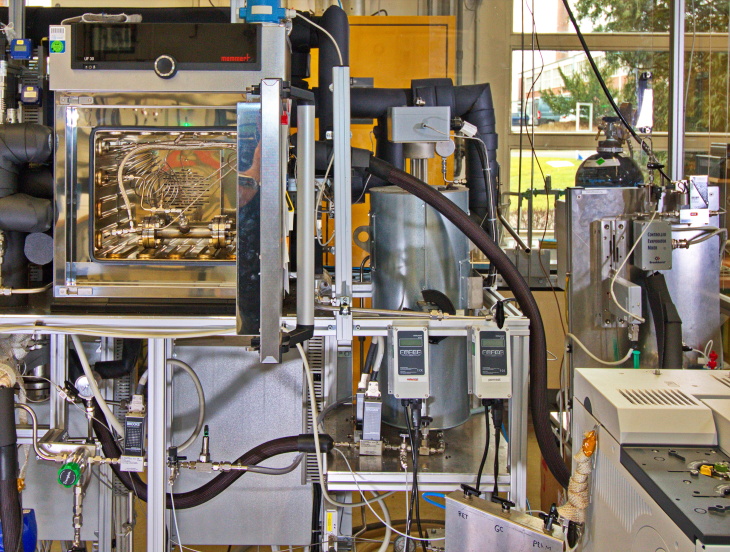
Image: Hereon/ S. Shishatskiy
Purpose:
The mixed gas high temperature facility serves for characterizing the permeation behaviour of polymeric membranes for gases or gas mixtures at high temperature, elevated pressure and the optional addition of water or organic liquid vapour into the flow.
Features:
o Mixed gas/vapour facility
o Feed pressure range: 5 to 25 bar abs
o Permeate pressure: 1 bar abs.
o Temperature range: 30 to 250 °C
o Feed gas (mixed gas) flow: ≤ 2 l/min (at 0°C, 1.01325 bar)
o Controlled evaporation of liquids (CEM-System): ≤ 30 g/h
o Permeate flow measured by mass flow meters
o Feed, retentate and permeate gas stream compositions determined by gas chromatography
o Optional gas sweep flow on permeate side
o Different test cells applicable, flat and tubular shaped samples, area 1 cm2 to 34 cm2
Gas permeation plant for module scale investigations
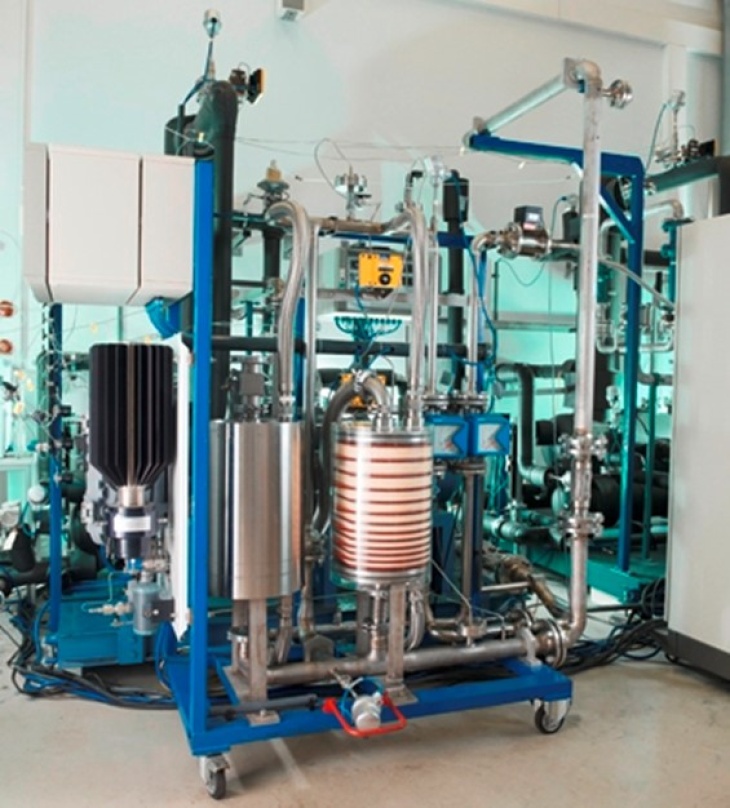
Image: Hereon/ general
Purpose:
Gas phase separations are important for various industrial applications. In order to access the operating performance of membrane based processes on module scale, the Hereon pilot plant can be employed.
Features:
o Gas Permeation pilot plant for the investigation of industrial sized membrane modules
o Liquid ring compressor and vacuum pump
o Gas mixtures can be supplied in feed vessel
o Vapour saturated feed gas by selection of service liquid (water or organic solvent)
o Possibility of mounting up to two membrane modules in parallel (max. ca. 50 m2 membrane area)
o Wide range of pressure ratios possible
o Composition analysis by gas chromatography
o Feed
- Maximum flowrate: 50 m3/h (at 0°C, 1.01325 bar)
- Maximum pressure: 5 bar
- Temperature: 8 to 30°C
o Permeate
- Minimum pressure: 33 mbar
- Suction capacity vacuum pump: 250 m3/h
Gas permeation plant for elevated pressures and extended temperature ranges
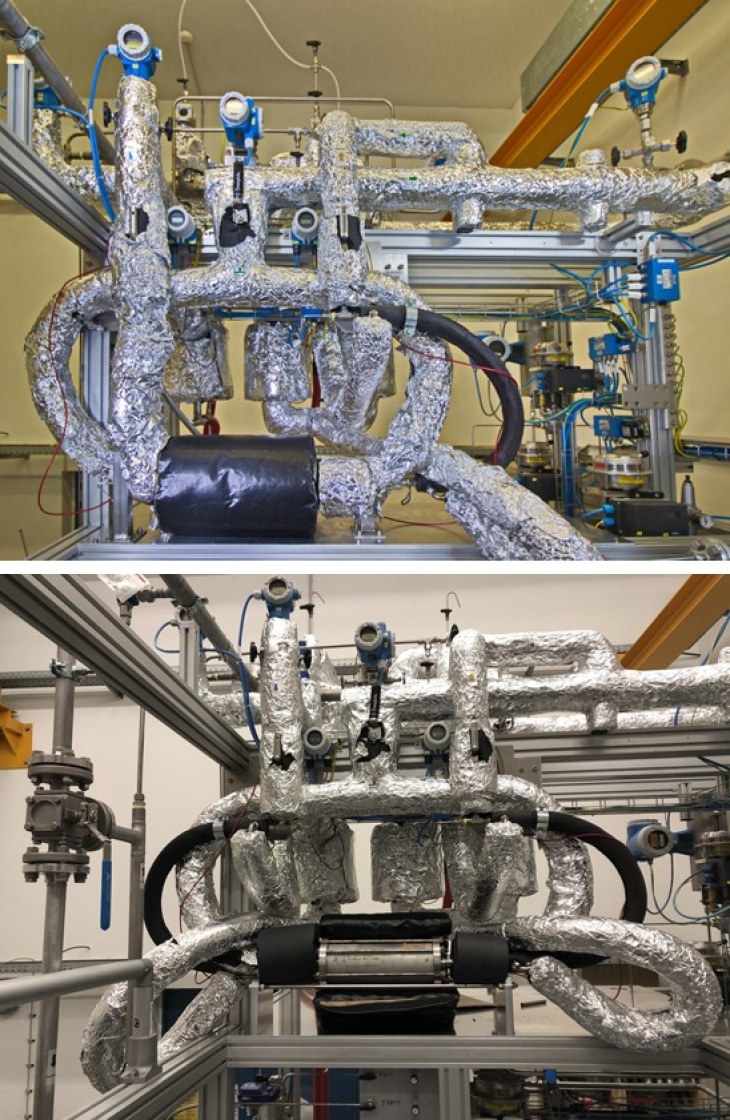
Image: Hereon/ S. Shishatskiy; T. Brinkmann
Purpose:
Investigation of membrane modules with up to 1 m2 membrane area for gas separation performance over extended operating ranges (temperature, pressure, flowrates).
Features:
o Closed loop design
o Layout according to ATEX
o Membrane module area of up to 1 m2
o Multicomponent gas mixtures
o Variation of feed gas mixture composition is possible during experiment
o Can account for “real life” effects: e.g. module scale, concentration polarization, Joule-Thomson effect
o Composition analysis by gas chromatography
o Feed
- Maximum flowrate: 32 m3/h (at 0°C, 1.01325 bar)
- Maximum pressure: 65 bar
- Temperature: -20 to 110°C
o Permeate
- Minimum pressure: 1.1 bar
Mobile gas permeation pilot plant for the separation of CO2 from flue gases
![Mobile gas permeation pilot plant for the separation of COsub]2[/sub] from flue gases](/imperia/md/assets/main/institutes/membrane_research/process_engineering/images/fittosize_730_0_0d21f7d728adadd73d839468792908ff_mobile_gaspermeationspilotanlage_fur_die_abtrennung_von_co2_aus_rauchgasen.jpg)
Image: Hereon/ T. Brinkmann
Purpose:
The separation of CO2 from various gas streams is one of the challenges of a modern industrialised society. Membrane processes allow for this separation. In order to investigate the feasibility of separating CO2 from various sources, this pilot plant can be employed in one or two stage membrane processes, allowing for CO2 purities in the separated stream of up to 75 mol.-% for one stage and up to 95 vol.-% for two stage operation. The pilot plant was built within the scopes of the projects METPORE II (03ET2016)and MemKoR (03ET7064) funded by the German Federal Ministry for Economics and Climate Action.
Features:
o Rigorous pre-treatment and temperature control of the feed gas
o One- or two stage (rectification cascade) operation
o 1st stage operates at ambient pressure with liquid ring vacuum pump providing the driving force, typical membrane are of high performance CO2 selective membrane: 15 m2
o 2nd stage uses permeate of 1st stage compressed by piston compressor, typical membrane are of high performance CO2 selective membrane: 1 m2
o Continuous data acquisition and possibility for remotely controlled operation
o Continuous composition analysis by infrared, paramagnetic and humidity sensors
o Feed
- Maximum flowrate: 80 m3/h (at 0°C, 1.01325 bar)
- Maximum pressure 1st stage: 1.2 bar
- Maximum pressure 2nd stage: 6 bar
- Temperature: 20 to 50°C
o Permeate
- Minimum pressure 1st stage : ca 30 mbar
- Minimum pressure 2nd stage : 1 bar