Techniques and equipment
Equipment | Features |
Scanning Electron Microscope LEO Gemini 1530 | Equipped with EBSD, EDX, WDX |
Scanning Electron Microscope Zeiss DSM 962 | Equipped with EDX |
Transmission Electron Microscope Philips CM200 | 200 kV, equipped with EDX |
Transmission Electron Microscope FEI Titan 80-300 | 300 kV, FEG, Cs-Correction, EFTEM/EELS, EDX |
Dynamic High-Temperature-Calorimeter Netzsch DSC404 Pegasus | DSC and spec. Heat up to 1650 °C |
Bähr Thermoanalytic | Specimen environment with dilatometry, DSC and deformation unit for in-situ diffracton experiments |
Leeco analysis system | Measurement of O2, C, N2 and H2-level |
Powder atomisation unit | PIGA and EIGA atomisation |
DS-Unit, Fa. Linn | Directional solidification of TiAl, titanium and other metallic materials |
Laboratory arc melting unit with cold crucible, Fa. Bühler | Casting of experimental alloys in batches up to 100 g |
Forging-Simulator DSI Gleeble 3500/3800 | Tension, compression and torsion up to 1350 °C |
Mechanical testing | Tensile testing up to 1000°C, creep experiments |
For the characterisation of the microstructure, constitution and defects in metallic and intermetallic alloys two scanning electron microscopes (SEM) with different analytical extensions (EBSD, EDX and WDX) and two transmission electron microscopes (TEM) are available.
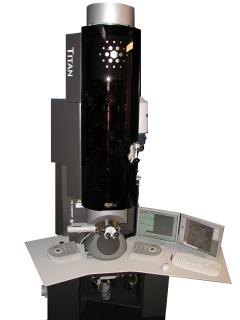
TEM FEI TITAN 80-300 with Cs-corrected optical system
The FEI TITAN 80-300 TEM with its aberration corrected electron optics is used for microstructure investigations with atomic resolution.
Alloy constitutions and phase transitions are investigated with a dynamic high temperature calorimeter. Additionally the department routinely performs diffraction experiments at the beamlines run by the Helmholtz-Zentrum Hereon at DESY. For this an in-situ specimen environment named FlexiTherm where specimens can be measured between room temperature and 1500 °C is employed. Heating rates up to 2000 K/s and cooling rates up to 4000 K/s are possible. Parallel to diffraction also thermal expansion by dilatometry and heat transfer by DSC (differential scanning calorimetry) can be measured.
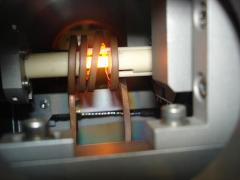
Induktive Heizung und glühende TiAl-Probe in der in-situ Probenumgebung FlexiTherm
For the mechanical characterisation of metallic and intermetallic materials we have three testing rigs for tensile tests up to 1000 °C as well as six creep rigs.
A powder atomisation unit for alloy powders on TiAl- and titanium-base is run by the department. This atomisation unit can be set up for two different atomisation methods:
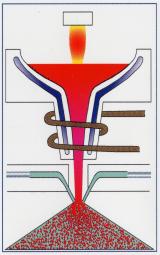
PIGA -Plasma Melting Induction Guiding Gas Atomisation- ceramic free with cold crucible and atomisation from a melt bath
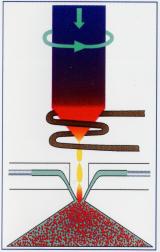
EIGA -Electrode Induction Melting Gas Atomisation- a ceramic- and crucible-free technique, where a pre-alloyed rod is molten and the flowing melt is atomised.
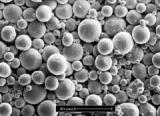
The powder of both techniques is spherical and of high purity. The set-up can produce powder amounts between 3 and 100 kg. The powder can be handled under argon atmosphere in glove boxes for sieving and packing to preserve the low oxygen levels.
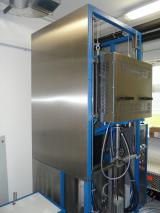
Solidification unit fordirectional solidification after Bridgman method
A DS-unit produced by Linn can make directionally solidified samples of TiAl-alloys and other alloy systems with length of about 20 cm and diameter of 11 mm. Another device for the production of experimental alloys up to 100 g is a cold crucible arc melting furnace for quickly providing test specimens to characterise the influence of different elements on the alloy properties. In a forging simulator Gleeble complex deformation states can be applied to specimens (e. g. tension, compression or torsion or combinations of these) to investigate the influence of forging conditions on the resulting microstructure.