Projects
Micromechanical properties of individual twins in Mg and Mg alloys
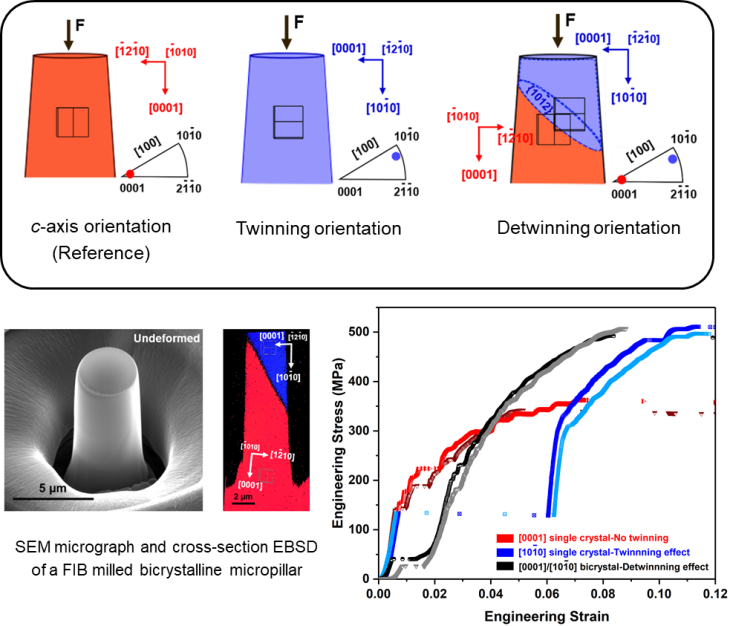
Photo: Individutal Twins. Lilleodden/Hereon
Magnesium and its alloys are known as superior metallic lightweight candidates in the transportation industry, where weight reduction is a top priority to decrease the fuel consumption and thus the CO2 emissions. Understanding the mechanical properties of these materials requires an investigation of slip and twinning mechanisms. This is very complicated at the macroscopic level, where deformation of a polycrystalline material leads to complex stress state and individual roles of slip and twinning cannot be truly decoupled from the collective response of several grains. In this project, focused ion beam (FIB) milling is used to machine micron-sized samples at single twin boundaries to explore the mechanical behavior of twinning with and without presence of alloying elements through microcompression testing. In this way, the effect of twinning on the stress-strain characteristics can be quantified, and linked to the corresponding deformation structures.
Micromechanical Investigations of Plastic Instabilities
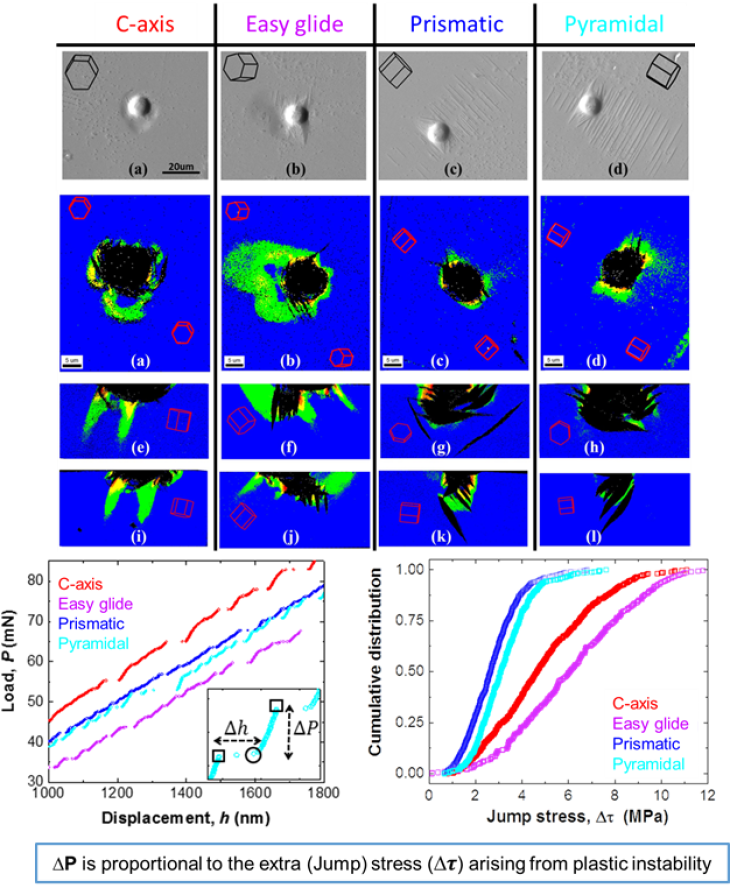
Photo:Micromechanical Investigation. Lilleodden/Hereon
Plasticity at the sub-micron scale is usually characterized by complex intermittent phenomena arising from both short– and long– range interactions between mobile dislocations and obstacles that lie along the glide path of the dislocations. Many of these intermittent phenomena (instabilities) are have direct influence on the mechanical behaviour of metallic materials. A typical example is the Portevin-Le Chatelier (PLC) effect; which is known to cause severe strain localization, reduction in ductility and formation of surface striations on several Al– and Mg–based alloys. A critical understanding of the underlying microscopic mechanisms that govern this phenomenon is necessary for designing alloys and process routes that mitigate it. In this project, insight into the underlying micromechanisms is gained by employing a combination of small-scale mechanical testing (nanoindentation and microcompression), in-depth microstructural characterization (TEM, in-situ TEM, ESBD) and modelling. In addition, nanoindentation based approaches are being developed to identify the relevant atomic species/obstacle types that promote the instabilities and to assess the underlying rate controlling mechanisms.
Micromechanical investigations of nanostructured composite materials
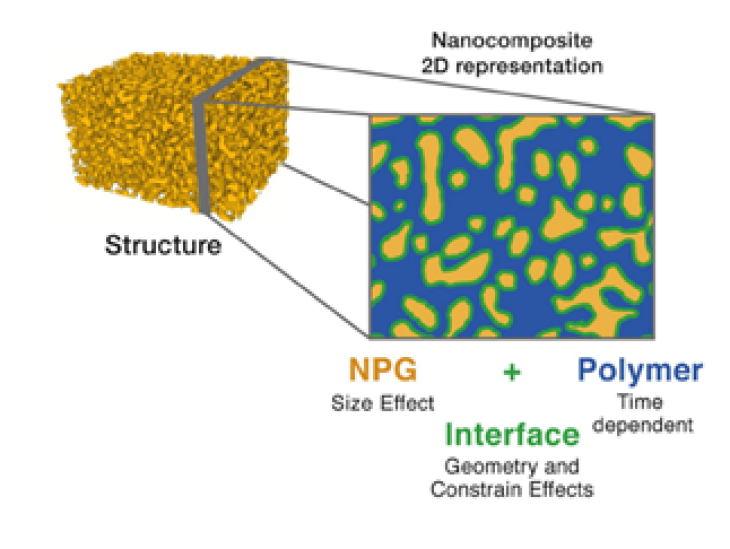
This research project aims to investigate microstructural length-scale effects to describe the mechanical behaviour of nanoporous gold (NPG)-polymer materials. The separated contribution of reinforcement phase, matrix and interface are addressed using a combination of scanning electron microscopy, transmission electron microscopy, focused ion beam (FIB) machining and nanoindentation-based mechanical testing methods. A novel methodology to separate the matrix phase and the fabrication of planar interfacial model samples supported a systematic investigation of the independent contribution that build up the composite overall response. The experimental results developed here are incorporated in mechanistically informed models.
Coupled electro-chemo-mechanical testing at the micron scale
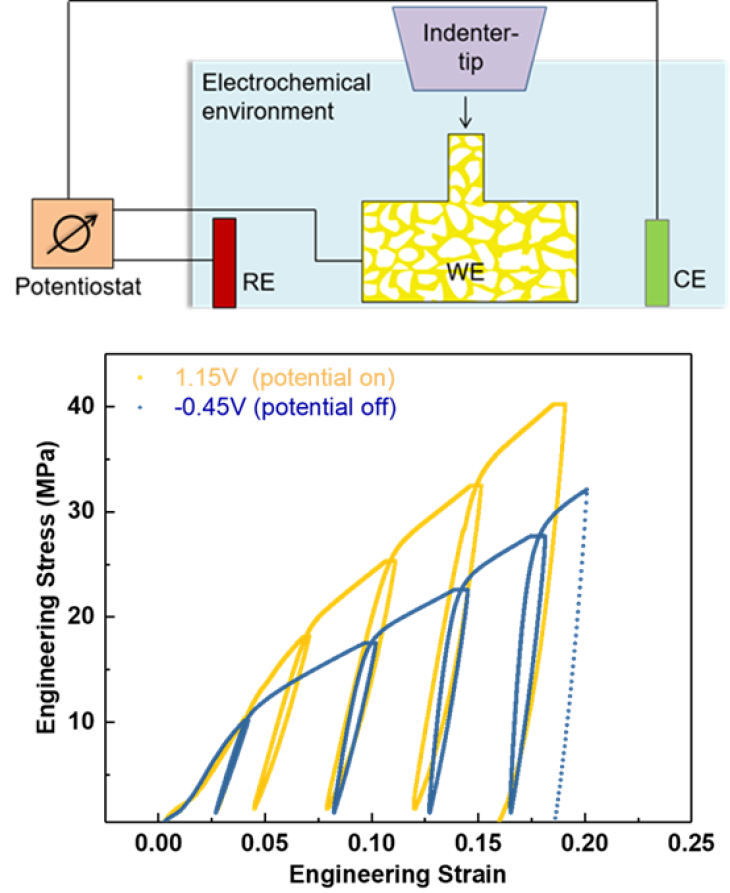
Photo: electro-chemo-mechanical testing. Lilleodden/Hereon
Nanoindentation and microcompression testing, during which samples are immersed in an electrolyte and the surface chemistry can be controlled by an applied potential, can be carried out by means of a modified nanoindenter with an electrochemical cell and potentiostat. Using this technique, mechanical behavior (e.g., elasticity and plasticity) and functional behaviors (e.g., actuation and sensing) of small, site specific volumes under oxidizing and reducing conditions can be studied.
Micromechanical investigations of structural alloys
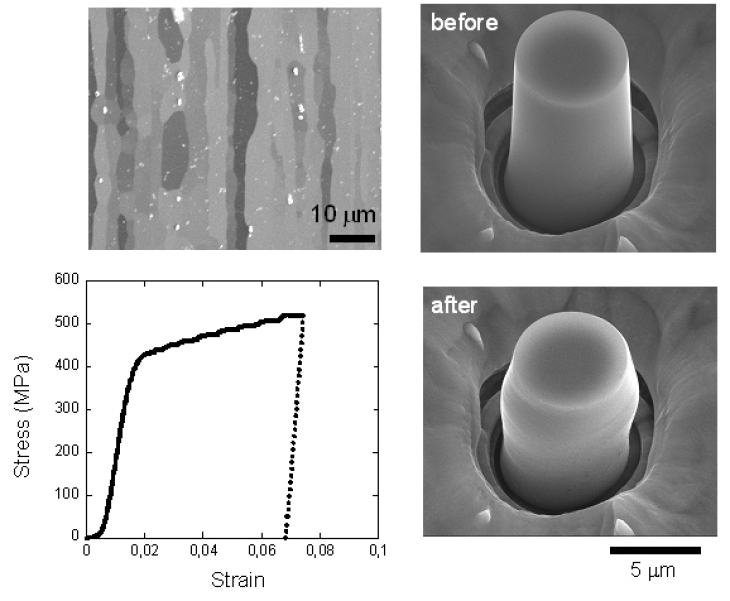
Our goal is to understand on a microstructural level the mechanical behavior of structural alloys using a combination of scanning electron microscopy, focused ion beam (FIB) machining and nanoindentation-based mechanical testing methods. In the given figure, we see an ion contrast image showing the anisotropic grain structure of a rolled Al-Li alloy sheet, along with SEM images of the FIB fabricated micro-column before and after compression testing and the corresponding engineering stress-strain curve.
Determination of material parameters for component characterisation via indentation instrumentation testing"
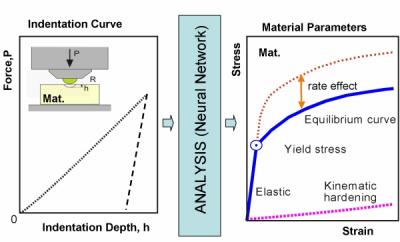
Photo: Indentation. Lilleodden/Hereon
New developments show that a multitude of material parameters for the description of elastic-plastic and/or visco-plastic material behaviour can be obtained via indentation instrumentation testing. Until now, these methods were successfully used in laboratory settings. For component characterisation, these methods have the advantage that material parameters can be obtained locally and nearly non-destructively at the surface of the component by measurement and analysis of the indentation curve.
The application of the method to components is not yet established, as components exhibit residual stresses; a property which is not yet considered to date in the methods. Aim of the work is to make the method ready for application to welded light-weight structures under consideration of residual stresses, as well as the special experimental conditions in components compared to laboratory specimens.